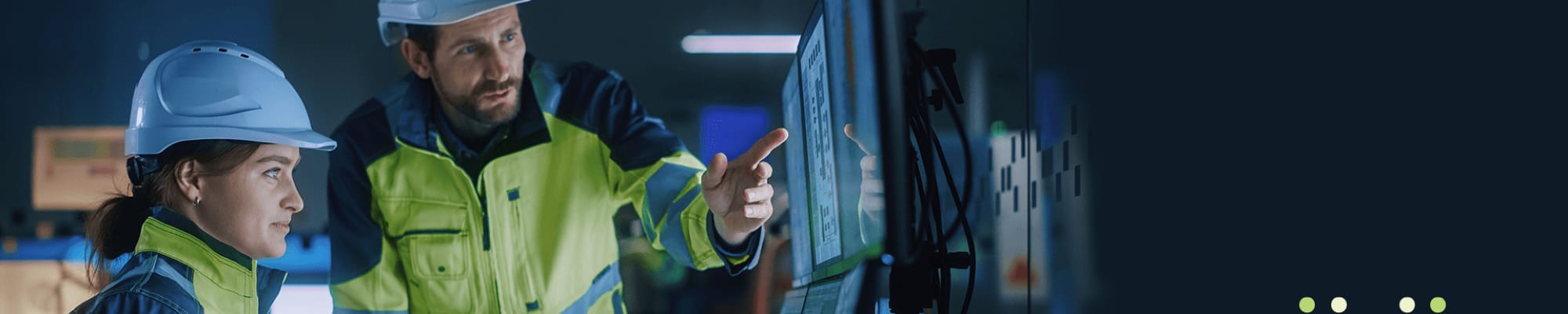
Environmental ratings and sustainability have become increasingly important and are becoming a key competitive differentiator in the market. Government regulations and investors urge companies to report their environmental impact; in fact, this has now become a vital part of their non-financial reporting requirements. Meanwhile, through digitalized and intelligent production, industrialization is evolving towards the fourth generation (industry 4.0), which aspires to attain higher levels of efficiency and productivity with less input and lower cost.
As a result of the above-mentioned factors and trends, many companies are adopting practices and policies that are intended to have a positive influence on the planet. There is a growing interest in implementing environmental sustainability principles in their day-to-day business operations and corporate responsibility. Today, many manufacturers are establishing this model to make their products and services more sustainable.
In this article, we are going to highlight how facility digitalization can help in achieving more environmentally responsible operations and meeting sustainability goals.
What is Facility Equipment Operations Digitization?
It is the networking of physical equipment used in managing the facilities' environment – such as Heating, Ventilation, and Air Conditioning (HVAC) equipment, lighting, refrigeration, site sensors, metering and controls – over the internet. Digitization is usually accompanied by applications (such as those that leverage Artificial Intelligence (AI) driven software) that facilitate centralized management of connected equipment.
With the right combination of connected technologies, coupled with an intelligent analytics platform, connected equipment components can talk to each other - making the connected system smarter. The sensors collect system and equipment level data and send it to a remote command center where this data is continuously monitored for tracking performance versus stated environmental objectives.
Using AI to monitor equipment and gather intelligence makes it easier to forecast equipment performance and lifespan before it is harmed or fails. This can aid facility management teams in more successfully performing preventative maintenance and addressing possible concerns before they become problems.
Artificial Intelligent is unique in that, unlike condition-based maintenance, it does not rely on pre-programmed algorithms. Instead, it allows the computer to find patterns, trends, and insights from large aggregate data sets. Artificial Intelligent systems can also update models used to make analytical predictions on facility performance and efficiency since they leverage data obtained from Internet of Things (IoT)-enabled sensors.
How Facility Digitalization Improves Environmental Goals
Key environmental program challenges include reducing carbon footprint by preventing energy inefficiencies, maintenance cost reductions and pollution prevention.
AI and IoT platforms have the capability to constantly monitor, analyze control operations, manage equipment performance, predict equipment issues and even offer prescriptive recommendations. Remote monitoring service teams can then work on those predictions and recommendations to ensure opportunities are acted upon to overcome environmental challenges.
- Carbon footprint reductions through energy efficiency. With interconnected systems, using AI-enabled solutions to improve energy efficiency and reduce carbon footprint is a classic use case of digitalization of equipment operations. HVAC equipment faults and the poor scheduling of systems are some of the sources of inefficiencies within buildings. Identifying waste and predicting energy inefficiencies before they accumulate and grow, from poorly performing or old equipment, enables manufacturers to save on energy consumption and report better efficiency. Optimizing equipment usage also improves the overall health of the equipment, which can reduce operating costs and delay replacement. Manufacturers can identify energy inefficiencies such as those caused due to improper economizer operation, malfunction of expansion valve and compressor/heater capacity inadequacy related issues. These issues can be addressed promptly to avoid wasted energy.
- Maintenance cost reductions. AI-enabled solutions typically deliver predictive analytics on equipment performance and offer remote-control capabilities to drive maintenance management. By leveraging cloud-based predictive AI analytics to monitor and manage the performance and condition of building equipment, manufacturers can address predicted failures to minimize equipment downtime and trigger maintenance actions promptly to reduce disruptions and cost of repair. These digital transformation processes help manufacturers move toward using a predictive maintenance approach. Manufacturers can take proactive actions based on the actual condition of equipment.
- Pollution prevention. Global Warming Potential (GWP) was developed to allow comparisons of the global warming impacts of different gases. Specifically, it is a measure of how much energy the emissions of one ton of a gas will absorb over a given period of time, relative to the emissions of one ton of CO2. With respect to the CO2 impact, the GWP describes the potential contribution to the greenhouse effect induced by the molecules present in a gas that has been released.
Early identification of HVAC equipment refrigeration leaks may be predicted with AI and IoT solutions, which helps to minimize the impact of such failure. Apart from reducing pollutants, this can also lower energy costs, enhance cooling system capability, and prevent the need for a total refrigerant replacement. These environmental challenges can be measured and reported with the data collected from the centralized software (usually a building energy management system or BMS). Using AI technology not only helps manufacturers collect more accurate data but also helps them in identifying useful improvement insights and acting on those insights to meet some of their strategic environmental goals.
For more on this topic, please email [email protected].
May 2022
Author
Yoganathan Murugesan, Manager, Industrial Practice at EcoEnergy Insights
Yoganathan leads the industrial practice solution of EcoEnergy Insights. He works on business strategies for various industrial segment for business expansion and support sales function. He is also responsible for offering AI and IoT based product solutions along with designing services for clients. Yoganathan is passionate for developing solutions that help clients reduce greenhouse gas emissions and improve overall facility energy efficiency.