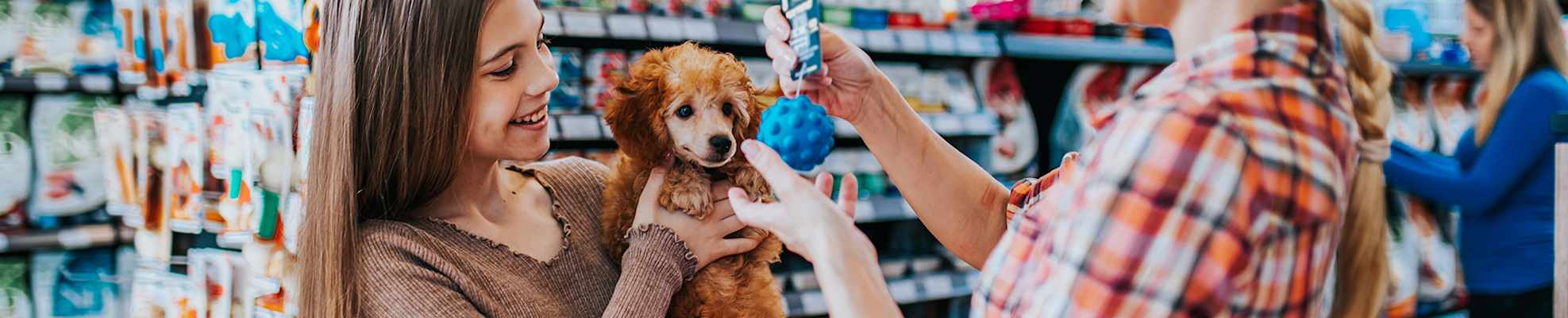
From department stores to grocery stores, customer comfort has always been important to retailers. One of the largest retailers in the U.S. was no exception. However, ensuring comfort while keeping energy consumption and maintenance costs low was a significant challenge for them. Through predictive maintenance, we helped them improve occupant comfort, ensure compliance, increase energy efficiency and reduce maintenance costs for over 1,500 of their stores. We also helped them maximize equipment uptime.
The solution that we deployed has three distinct aspects:
- Proactively analyzing the equipment health across the stores through CORTIX™, our AI-enabled Building IoT platform
- Performing remote corrections and making intelligent decisions on when to carry out field dispatch, before the problems mature and start impacting store policy compliance
- Transforming the field service process to improve effectiveness of maintenance through data
In the past, the use of predictive analytics required a huge quantity of data, and processing it was a costly and time-consuming process. With the progress of technology and emergence of powerful platforms like CORTIX, one can perform rigorous analysis using less time and cost. Before working with us, the retailer used to reactively dispatch technician(s) after receiving complaints from a store. The technician would visit with very little information, at times resulting in a waste of time and money as non-persistent issues would not show up during the visit.
We transformed this process from reactive to proactive, by designing advanced algorithms around predictive maintenance and applying those to the retailer’s equipment data using CORTIX. Instead of waiting for scheduled maintenance or equipment failure, CORTIX helped us predict when the equipment performance would begin to deteriorate and when it might fail. Our data scientists and analysts ensured technician visits for such equipment were planned in a way that costs were minimized in two ways. Technicians were given enough information on all the problems beforehand, which enabled them to carry the necessary parts and avoid another trip to get those parts after diagnosing the problem. Technicians were also informed of issues in other equipment at the same store, thus avoiding multiple visits to that store.
We helped reduce costs by about 26% for over 22,000 energy-consuming equipment in over 1,500 stores.
Predictive maintenance can help optimize comfort, efficiency, maintenance and other business objectives for any type of building(s) – including hotels, banks, restaurants, manufacturing plants and more.
August 2019
Authors
Ravi Meghani, General Manager
Ravi has been leading innovations in managing non-IT devices at EcoEnergy Insights for the last 11 years. He is responsible for architecting award-winning propositions across a wide range of business outcomes like energy management, process efficiency, occupant comfort, and operational excellence for retail and water utilities sector. An avid tech buff, Ravi has been passionately building solutions in IoT, analytics, managed services, IT infrastructure, security and networking. While bringing depth to context-based strategies, he enables faster realization of benefits for clients globally. Ravi holds a Bachelor’s degree in Electronics Engineering, and has keen interest in the areas of sustainability and conservation.
Mansoor Ahmad, Managing Director
Mansoor Ahmad has been influencing the future of Building IoT through EcoEnergy Insights’ disruptive innovations. Mansoor is responsible for steering a start-up incubated in 2009 within an IT Services company, into EcoEnergy Insights of today - A leading provider of outcome-based services to some of the world's largest enterprises in over 20 countries across the globe. Under his leadership, EcoEnergy Insights developed and launched the CORTIX™ platform and associated digital and digitally enabled solutions. Mansoor holds a bachelor’s degree in Engineering is passionate about using technology to make the world a better place to live in.