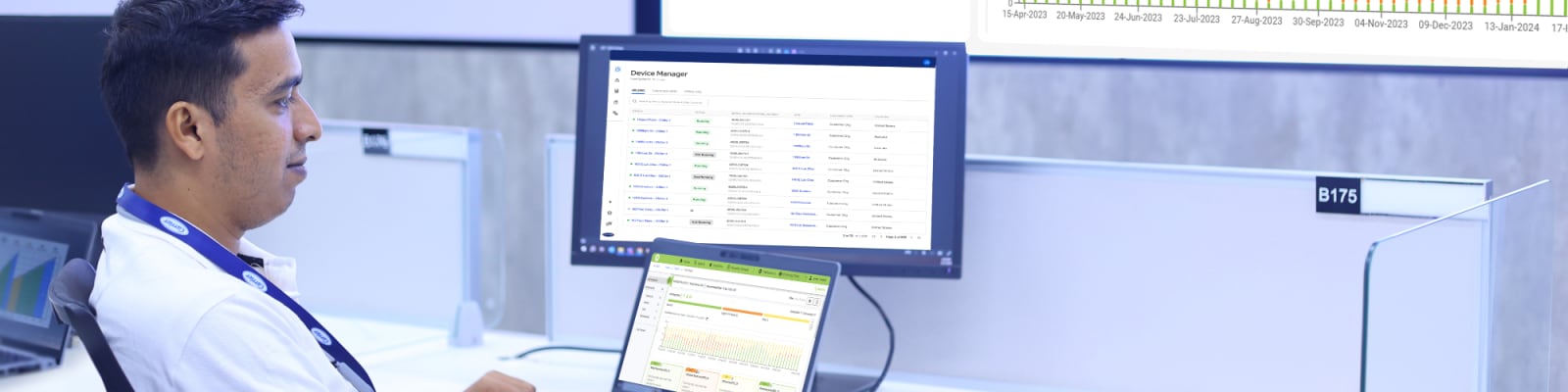
Heating, Ventilation and Air-conditioning (HVAC) units are critical to maintaining indoor environments, which in turn are critical to providing a great experience to employees and customers. There have been numerous advancements in the technologies used in HVAC equipment in the recent past. While this has improved their capabilities, it has also made operations and maintenance increasingly sophisticated. The maintenance of equipment significantly impacts the ability to deliver the cooling required as well as how efficiently it does so. The units require proper and timely maintenance to perform at optimum levels, avoid failure and any resulting interruptions to business operations. There’s a link between the degrading performance of equipment and the costs involved to repair as shown in Figure 1.
Figure 1: Rising costs with degrading equipment performance over time
Typically, building facility management teams would be alerted to degrading equipment performance with alarms. They would then have to observe the data, plan on how to act on the available data and address a particular issue that is responsible for an alarm. This is reactive in nature and typically, by the time an alarm has gone off and been noticed – from among other alarms that may also be going off elsewhere – the window to fix at a lower cost has passed. This would result in making more expensive interventions or even having to replace costly parts. This further increases costs with loss of revenue caused by shutdowns to repair the equipment.
With remote services powered by Artificial Intelligence (AI) and the Internet of Things (IoT), teams can now be more proactive. The ability to use data to anticipate potential issues with predictive analytics enables us to address issues before they manifest into larger problems – aiding in decision making to reduce energy and maintenance costs and ensuring business continuity.
Proactive actions with the Abound Insights Platform and BluEdge Command Centers
The Abound Insights platform, has been designed to not only help anticipate issues but enable users to be proactive with easy-to-understand actionable insights. The BluEdge Command Centers – teams of skilled analysts, data scientists and domain experts – work with the insights and recommendations to realize the opportunities to optimize equipment performance, that have been uncovered by the platform.
In Figure 2, you can see how the platform’s interface (available on mobile and desktop) give color-based indications that align with the main 4 stages of degradation, named S1 to S4. Green is used to indicate that the equipment is performing well. Yellow is used for the early stages of degradation when the business still has time to plan maintenance actions. Orange is used when the degradation has progressed further and needs urgent attention. Red is used when equipment has failed and needs repair. The platform gives prescriptive recommendations in natural language, based on the stage, for users to be able to act on the same and correct the issue before it progresses to a further stage. The platform uses data to anticipate issues and then autonomously correct them where it can before it highlights that human intervention is required to address a growing problem. The platform labels actions as either “urgent” or “plan” to enable users to prioritize actions easily. This is especially useful in a retail enterprise where there are a large number of actions required across equipment at a large number of stores.
Figure 2: Stages of degradation (S1-S4) with mapping as in the Abound Insights platform
The BluEdge Command Centers accesses the recommendations to plan actions proactively and address issues remotely. The Command Centers prioritize recommended actions based on severity, from among hundreds and even thousands of suggested actions to focus on those that will deliver the highest impact. The teams then either remotely address issues by logging into systems on site or create work order for field teams to act on. They would collate problems to be addressed at a building, so that multiple fixes could be attended to in one visit. By creating detailed work orders, field teams would travel with the desired parts to address all the issues at site not cause further delays or rise in costs with multiple visits for a fix. The ability to do a First Time Fix (FTF) increases drastically.
Figure 3: Sequence of actions to proactively correct issues
The sequence of actions as shown in figure 3 enable businesses to have continuity of operations and not face escalating costs when issues arise. The equipment performance issues are addressed almost as soon as they are detected in some cases and in others, planned proactive actions take care to address them before they manifest into larger and more expensive problems.
AI and IoT driven remote services in action
For 3 large retailers, with over 4,200 connected stores combined, across the USA and Canada, the BluEdge Command Centers used the insights and recommendations from the Abound Insights platform to achieve the following in 2023:
- Autonomous actions: Over 142 million. Certain defined actions such as the calibration of sensors and changing of setpoints, were carried out directly and autonomously by the platform.
- Remote resolutions reduced maintenance truck rolls: Certain predictive actionable insights from the platform were acted upon remotely by the teams at the BluEdge Command Centers by logging into the Building Management Systems. These actions were either pre-approved by the retailer or after consulting with them. The proactive actions for the year 2023 amounted to approximately 117,000 and the command centers could track those completed and those which were still in progress, allowing the retailer to prioritize and plan actions effectively. In addition, there were 25,525 quick response actions for the year and these were done in a manner that enabled saving on truck rolls. Quick response actions are those involving responding to calls or complaints from the stores. The team’s primary focus was on optimizing store equipment operations through resolving issues remotely as much as possible. Field teams were to be dispatched only when necessary. This approach enabled resolving issues more quickly and effectively, whilst also avoiding the associated emissions from the trucks that would have had to visit multiple stores on multiple occasions.
- Intelligent Field actions addressed site issues holistically with reduced repeat visits: Field teams had all they needed for a First Time Fix –
- detailed work orders from the command centers that covered other equipment at the same store to reduce time spent troubleshooting and
- access to live data to see performance at the site, through the Abound Insights platform mobile app. This app also allowed looking at daily and hourly history for ease of diagnosis and repair.
- In year 2023, the command centers were able to track approximately 86,000 work in progress field jobs and complete the same without any repeat visits, thus preventing equipment failures and reducing the number of truck rolls.
As a result of these measures, there has been an over 12% improvement in health of the connected equipment, as compared to 2022.*
These actions facilitated a reduction of the spend in maintenance costs, the amount of downtime and the associated emissions from truck rolls to the stores.
As a result, this combination of platform and command centers enabled the retailers to be more proactive in their operations and contribute to reducing emissions from energy consumption and maintenance of equipment, thus making their store operations more environmentally friendly too.
*Of the total number of equipment performance issues in a year, 10.27% were urgent issues in 2023 compared to 11.78% in 2022.
APRIL
2024
Author
Shawn Menezes, Senior Manager, Brand and Product Marketing
Shawn Menezes leads the brand and product marketing function at Carrier Abound. He works on strategies and campaigns to drive the brand and products forward. He is passionate about contributing to the fight against climate change and communicating how technology can make energy-intensive building operations more sustainable.