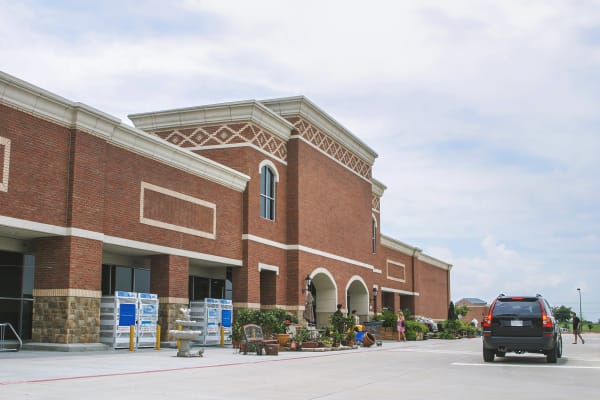
A retailer reduces the environmental impact of operating its over 16,800 stores
The Client
An American chain of discount variety stores that operates in over 45 states in the United States. The retailer aims to offer customers value at nominal prices and a fun shopping environment.
The Challenge
The retailer encountered challenges in efficiently managing their energy consumption across their extensive store network and needed support with monitoring their energy usage. Additionally, they found it difficult to organize and prioritize the high volume of work orders from their stores, which impacted the timely completion of tasks.
To overcome these challenges, the retailer entered a strategic engagement with Carrier Abound, initially spanning over 1,100 stores. A comprehensive solution featuring the BluEdge™ Command Centers was implemented. The centers are made up of specialized teams of skilled analysts, data scientists and domain experts and provide 24/7 support for streamlined store operations. The support included remote technician assistance, effective equipment configuration management, and prioritization strategies for enhanced operational efficiency. The collaborative engagement also aimed at advancing the retailer's teams' proficiency in technology and Building Management Systems (BMS).
The teams at the BluEdge Command Centers applied a systems-thinking approach – drawing from their knowledge of multiple equipment categories, the retail industry, and expertise in information technology and building controls – to holistically solve problems. The team’s primary focus was on optimizing store equipment operations through proactively and remotely resolving issues. Field teams were dispatched only when necessary and even then, work orders were combined to minimize dispatches to the same store. The work orders were also more detailed, enabling the technicians to be more productive when at the stores. This approach enabled resolving issues more quickly and effectively, whilst also avoiding the associated emissions from the trucks that would have had to visit multiple stores on multiple occasions.
The team managed a monthly average of over 3,800 HVAC, lighting, and control work orders over a span of 3 years, where they supported with thorough investigations referencing the store history and live testing. They filtered out duplicate issues and provided detailed per-equipment reports for resolution. The implementation of a measured resolution time threshold prioritized emergency work orders, which enabled the quick resolutions of critical issues. Support to field technicians was provided through robust troubleshooting and historical data presentation. There were two levels of support set up, one for general and one for advanced cases, enabling appropriate support for different levels of complexity of work orders.
The team also addressed challenges related to diverse weather conditions, developing a comprehensive weather reporting and response strategy. They delivered weekly summaries of forecasted weather conditions and recommended actions to create comfortable environments in stores. This proactive approach extended to monitoring store statuses during severe weather events, enabling the retailer to make informed decisions on how to run and support affected stores.
In 2022, the retailer began participating in Demand Response (DR) events, where they helped adjust store settings during these events, successfully transitioning most notifications to a DR aggregator's service. This strategic move enhanced responsiveness, especially during events with shorter notification windows, demonstrating a commitment to supporting the grid. This measure also enabled the retailer to earn rebates.
The Result
Carrier Abound enabled the retailer to monitor its equipment effectively and optimize equipment operations and maintenance. The engagement quickly scaled up to over 16,400 stores within two years of commencement.
These are the results achieved in the year 2023, with the engagement spanning 16,800 stores:
- Estimated USD 7.1 million* saved by avoiding over 14,200 truck rolls.
- 85,000+ schedule changes were made. The changes were made to HVAC and lighting equipment operations, important for managing the customers’ experience in stores. The support helped the retailer to be agile and energy efficient.
- 83,500+ technician calls handled. The technicians were provided with critical information to achieve higher first-time resolutions.
- Average 99% Service Level Compliance to emergency work orders within the specified resolution time, which helped the retailer swiftly address critical issues.
- 300+ DR events handled saving energy costs for the retailer and earning rebates.
Through this engagement, the retailer has transformed the way they run their operations – from being reactive to being proactive, from focusing on individual stores to focusing on the collective network and from using only field actions, to using remote and field actions to solve problems.
This also enabled the retailer to reduce the emissions of over 2,300 metric tons of CO2 emissions** from truck rolls, in addition to emissions from wasted energy, thus reducing the negative environmental impact of its operations.
*Disclaimer: This estimate is calculated based on the industry standard of USD $500 per truck roll.
**As calculated from https://business.edf.org/insights/green-freight-math-how-to-calculate-emissions-for-a-truck-move/