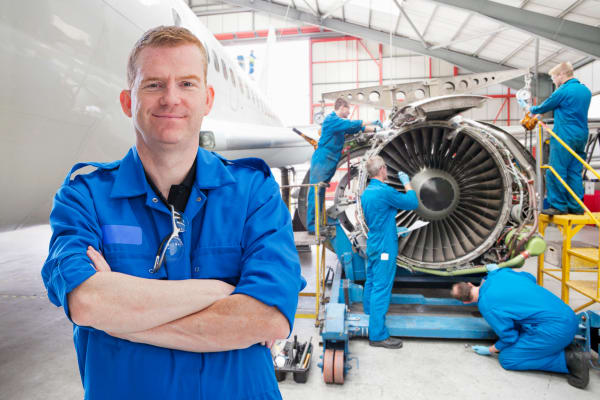
The Client
An American aircraft engine manufacturer that designs, manufactures and services aircraft engines and auxiliary power units.
The Challenge
A large manufacturing facility of the organization has a gas turbine-based Cogeneration plant for generating steam to meet the heating needs of the facility. The capacity of the Cogeneration system is 8 MW and steam is generated using Heat Recovery Steam Generator (HRSG) of 30,000 lbs./hr. capacity. The steam from the HRSG is also used for operating a Vapor Absorption Chiller, to generate chilled water to meet the cooling needs of the facility. This facility had over 300 facility equipment, such as Heating Ventilation and Air-Conditioning (HVAC) equipment apart from the over 500 production equipment in the production process.
During the colder months of the year, the excess steam from the Cogeneration plant was used to heat the facility. During the warmer months, the need for heating would be low, due to the relatively higher outside air temperature. As a result, the steam generated during these months is more than necessary and the excess would be released to atmosphere. Due to this release of steam, there would be a lack of sufficient heat source to operate the vapor absorption chillers. Hence, the vapor absorption chillers would be underutilized. At the same time, to meet the cooling load requirements, the organization would spend on using the electric vapor compression chillers. As a result, there were energy and monetary losses.
To overcome the above challenge, the manufacturer engaged Carrier Abound. Our experts were tasked with identifying and implementing strategies to save energy and reduce the environmental impact caused by the steam generation process.
The Solutions
Carrier Abound’s engineers analyzed the data from the cogeneration system to provide the client with data-driven insights for strategic decision-making.
Based on the analysis, it was noticed that vapor absorption chillers are underutilized due to insufficient heat source as most of the steam is released to atmosphere. Since the heat source is insufficient or inconsistent, the vapor absorption chiller is unable to generate the required cooling capacity to meet the cooling load requirement, hence electric based vapor compression chillers are operated in sync with vapor absorption chiller.
Due to inadequate control logic systems and a partial amount of steam being released to atmosphere, the vapor absorption chiller did not respond effectively to changing conditions, leading to its underutilization. Carrier Abound’s analysts and experts from their BluEdge Command Centers identified the root cause of the problem, defined action plans and ensured
insights were implemented in a timely manner to help maximize the utilization of vapor absorption chiller during summer and spring seasons and allowing for better utilization of the cogeneration plant.
The Result
The analytics from Carrier Abound improved the capacity utilization of the cogeneration plant. There was significant reduction in the release of vent steam into the atmosphere. This is more environment friendly. Also, the client was able to implement the optimization strategies without facing any downtime.
The partnership with Carrier Abound enabled over 3.2 million kWh units of electricity savings in 2023. This is equivalent to 2,235 metric tons of carbon dioxide emissions.
To overcome the above challenge, the manufacturer engaged EcoEnergy Insights. Our experts were tasked with identifying and implementing strategies to save energy and reduce the environmental impact caused by the steam generation process.