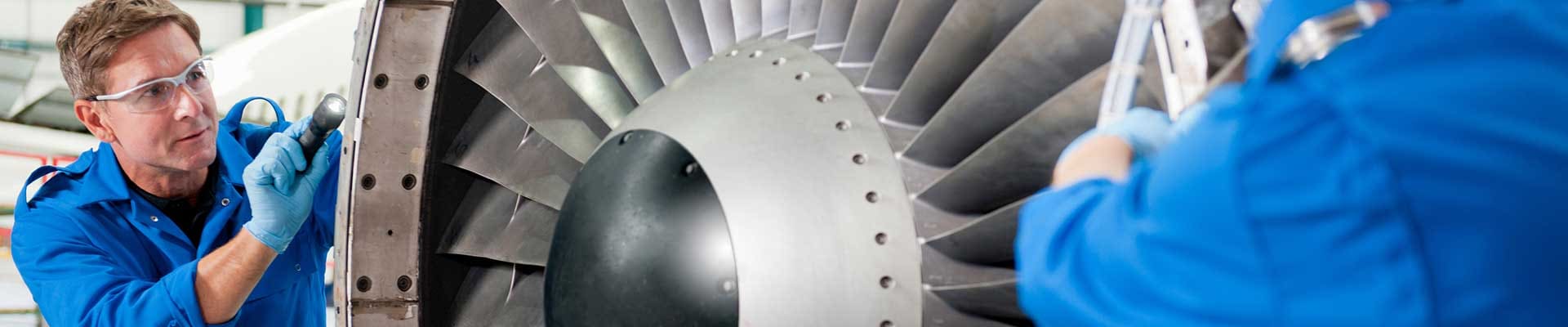
An aircraft engine manufacturer uses artificial intelligence to transform facility operations in large manufacturing facilities
The Client
A subsidiary of one of the largest aerospace, intelligence services providers, and defense manufacturers in the world. The client is an American aerospace manufacturer with global service operations and their aircraft engines are widely used.
The Challenge
As part of their corporate social responsibility initiatives, the manufacturer was looking to optimize its operations to reduce greenhouse gas emissions (GHG). Presently these targets were planned to be achieved through retrofits and upgrades. At the same time, the manufacturer was looking to reduce capital expenditure and wanted to adopt new technologies like Artificial intelligence (AI) and Internet of Things (IoT) to reduce operations costs and improve energy efficiency across their manufacturing and office spaces.
To achieve these objectives, the aircraft engine manufacturer engaged with Carrier Abound.
The Solution
Carrier Abound implemented a solution that leveraged the Abound Insights platform, a proprietary AI and IoT platform that constantly monitors and analyzes facility equipment performance, predicts equipment issues and offers prescriptive recommendations. By collecting and analyzing data on a continuous basis from the connected equipment, the platform identified changes in equipment behavior. It would then provide appropriate recommendations, in natural language, to correct issues and prevent them from growing into larger problems.
The integrated solution of hardware, platform and remote services, addressed the objectives of reducing energy consumption, improving equipment health and availability, reducing maintenance costs, and managing demand for facilities. The solution combined energy data, equipment operations, sensors, and weather data to drive down energy, GHG emissions and operation costs.
The manufacturer’s key 12 mixed-use buildings (manufacturing, once and R&D) in a single campus were onboarded to the Abound Insights platform, during which all HVAC, Lighting, and other facility equipment, connected to the building management systems (BMS) were integrated with the platform to create an intelligent infrastructure network. The Abound Insights platform provided unprecedented visibility into facility operations around equipment performance, post-maintenance interventions. It also helped increase the overall comfort and IAQ compliance levels across the buildings.
The insights and recommendations from the platform were prioritized and converted into a periodic report by our expert advisory team from our BluEdge™ Command Centers. Our experts used predictive actionable insights from the platform to define action plans and ensure implementation of insights in a timely manner.
The combination of the Abound Insights platform and the advisory experts helped in making the facility operations more proactive and efficient, leading to continuous savings and operational improvements.
The Result
This engagement helped address the challenges and yielded the following results across the 12 buildings in a single campus a year:
- Greenhouse gas emissions reduced by over 4,000 MT CO2e
- 2 million kWh units of electricity savings
- 241 thousand therms unit of gas saved
- 0.96 million kWh units of electricity optimized through scheduled corrections
- 129 thousand kWh units of electricity optimized through temperature setback during unoccupied hours
- 73 thousand kWh units of electricity optimized through AHU duct static pressure optimization
- Less than 12-month payback on the investment into the program