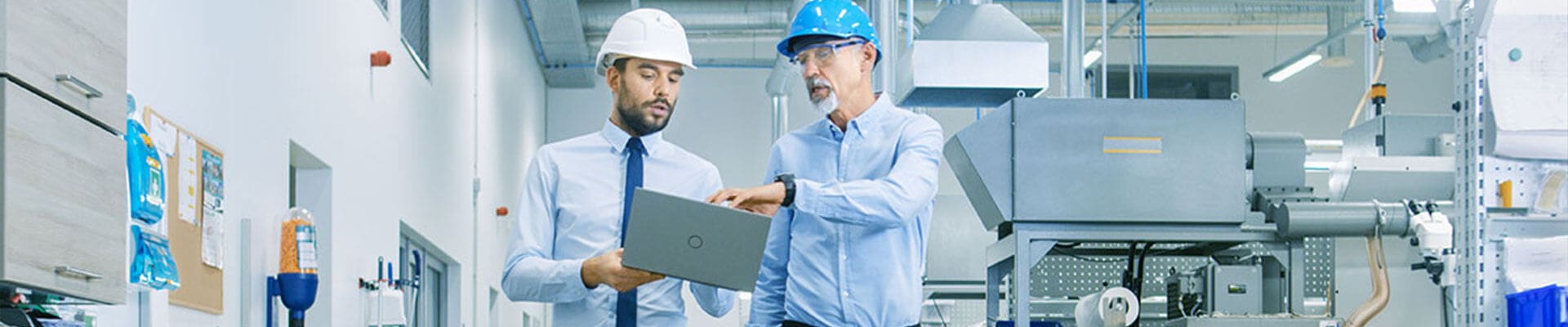
Transforming the HVAC equipment operations of a manufacturing plant
The Manufacturing Plant
One of the world’s leading players in heating, air conditioning and refrigeration solutions operates a large manufacturing plant in the USA, for producing their products for the residential market. This facility has been operational for over five decades and is spread across an area of 900,000 square feet, churning out over 1.2 million units annually.
The Challenge
The manufacturing plant faced multiple challenges in managing its resources and maintaining operations efficiently. Firstly, the frequent breakdowns of the heating, ventilating, and air conditioning (HVAC) equipment increased operational costs as well as negatively affected occupant comfort. The difficulty in identifying issues with the equipment performance hampered the overall efficiency of the plant. Secondly, the facility struggled to meet its sustainability target of 3% reduction in greenhouse gas emissions.
The complexity of the client’s manufacturing process and the distributed layout of equipment intensified the challenge even further. In order to combat these issues, the client engaged with Carrier Abound.
The Solution
Carrier Abound liaised with the client’s engineering team to understand the plant’s operations and the team studied available data from all existing building automation and energy management systems.
Upon analyzing the data gathered from the systems, the Carrier Abound team concluded that the existing systems were unable to provide visibility into the equipment performance and hence, the plant could not be actively monitored. The team then deployed the Abound Insights platform at the manufacturing plant. Data from all equipment and systems at the plant was fed to the platform. Upon complete integration, the platform was processing over 700,000 data records per day from over 8,200 unique data points. The platform provided actionable insights on three aspects of the equipment’s performance - health, availability and efficiency. Using these insights, a team of data scientists and domain experts at the BluEdge™ Command Centers discovered energy wastage scenarios and implemented over 30 HVAC controls-based strategies. This helped in managing resources while adapting to a more sustainable process.
The Result
The Abound Insights platform transformed the manufacturing plant’s maintenance processes by making them proactive. The platform predicted issues that could lead to equipment failure. These issues, when attended to promptly, enabled the plant to avoid problems that typically led to equipment downtime.
A fortnightly summary of deviations and recommended improvisations were submitted to the client as ‘work lists’. These work lists enabled the plant manager to avoid energy wastage. These actions were carried out either by the Command Center team remotely or by the client’s technicians.
Besides increasing the efficiency of the plant operations, the Abound Insights platform empowered the plant maintenance manager with critical insights on equipment performance post a service activity. This enabled them to determine whether the issue had been correctly addressed or not, thereby ensuring the effectiveness of the maintenance activities.
Within six months of the integration with the Abound Insights platform, the plant was able to achieve more than the targeted GHG (greenhouse gas) emission reduction.
Here’s a look at the improvement in six months:
- 5.5% average energy savings
- 9% average reduction in gas consumption
- 6.3% reduction in CO2 emission
- 22% improvement in thermal compliance
- .